Total risikovurdering af maskiner sikrer medarbejderne på Orkla Confectionery & Snacks Danmark A/S
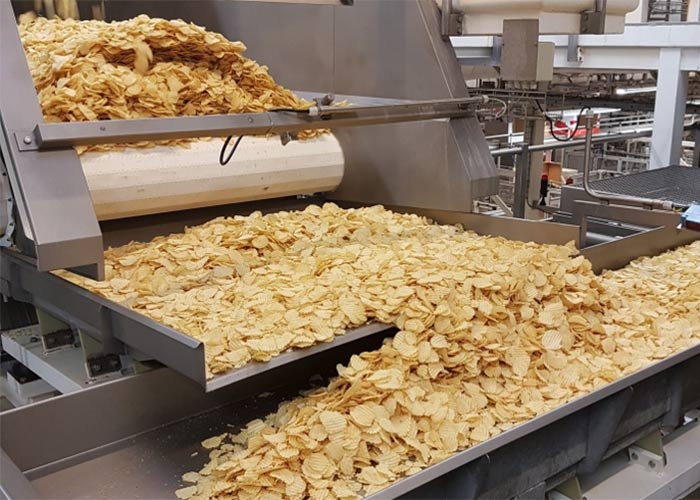
(som kendes under navnet KiMs). For at sikre, at ingen medarbejdere udsættes for risici i produktionen, har Supply Chain Director Jette Bruun igen igangsat en total risikovurdering af produktionsudstyret.
Selvom chipskongen Jørgen er gået på pension, er der heldigvis fortsat gang i både skrælle- skære og pakkemaskiner på Orkla Confectionery & Snacks
Ved at lave en total risikovurdering af vores produktionsområder sikrer vi, at vi hele tiden holder fokus på vores medarbejderes sikkerhed og sundhed, samtidig med at vi tager vare på vores omdømme som en god og sikker arbejdsplads. Når vi også involverer arbejdsmiljøorganisationen og giver dem en rolle og et medansvar både i de daglige og i større arbejdsmiljøopgaver skaber vi de bedst mulige forhold for medarbejdernes trivsel og sundhed.
Risikovurderingen er udført med deltagelse af både interne medarbejdere og med ekspertise udefra. Fra Orkla Confectionery & Snacks har vedligeholdelseschef Jesper Lauvring Hansen og to arbejdsmiljørepræsentanter, Anders Lynfort og Klaus Blæsbjerg Møller deltaget, mens faglig ekspertise er hentet i Joblife hos arbejdsmiljøkonsulent Rune Pedersen med bistand fra Rasmus Skov, som er maskinmesterpraktikant hos NIRAS. Sammen har de gennemført risikovurderingen af alle maskinanlæg på Orkla Confectionery & Snacks, som har to fabrikker i Danmark, hvor der produceres hhv. chips / snacks og nøddeprodukter.
I Orkla er der stor opmærksomhed på de enkelte virksomheders arbejdsmiljøindsats og resultaterne heraf. Det betyder, at Orkla Confectionery & Snacks minimum hvert 3. år opdaterer sine risikovurderinger for alle områder i produktionen. Desuden laves der løbende risikovurderinger ved installation af nye anlæg med deltagelse af både teknikere og kommende operatører på anlæggene.
Værktøjet til risikovurderingen
Når en så sammensat maskinpark, som Orkla Confectionery & Snacks har, skal risikovurderes, så ses der selvfølgelig først og fremmest på maskindirektivet, men derudover inddrages også de ergonomiske forhold og den interne færdsel i vurderingerne, da det ofte er her, at der er størst risiko for arbejdsulykker eller arbejdsbetingede lidelser.
Når der risikovurderes på Orkla-koncernens virksomheder, udfyldes et skema med følgende overskrifter:
- Afdeling
- Linje
- Maskine
- Opgave (fx ”arbejde ved rullebaner øverst på anlæg”)
- Identificeret fare (fx klemning)
- Overholdelse af lovgivning (ja / nej)
- Iboende fareniveau (rød/gul/grøn, hvis der overhovedet ikke var sikkerhedsmæssige foranstaltninger)
- Eksisterende sikkerhedsmæssige foranstaltninger (fx afskærmning på dele af maskinen, uddannet personale mv.)
- Nuværende fareniveau (rød/gul/grøn)
- Vurdering af, om fareniveauet er acceptabelt (Ja / nej)
- Etablering af yderligere sikkerhedsmæssige foranstaltninger (fx yderligere afskærmninger, hjælpemidler eller adfærd mv.)
- Kommende fareniveau (rød/gul/grøn)
- Ansvarlig person
- Deadline
- Dato for den faktiske afslutning af risikovurderingen
Samtidig skal man i risikovurderingen forholde sig til forholdene, både under drift, ved reparation og under rengøringen samt eventuelle forhold i en beredskabssituation.
Orkla Confectionery & Snacks
Maskinparken hos Orkla Confectionery & Snacks består bl.a. af anlæg til modtagelse af kartofler, som enten kommer direkte fra avlerne, eller fra lagre i Danmark og Tyskland. Når kartoflerne køres ind på virksomheden, bliver de først kvalitetskontrolleret på ”Kartoffellaboratoriet” inden de køres videre enten til det lokale lager eller direkte i siloer og dermed klar til produktionen.
Kartoflerne vaskes og sorteres, skrælles og sorteres, snittes, steges i solsikkeolie og sorteres, inden de køres op på ”broen”, hvor de krydres og afvejes til den aktuelle posevægt.
Pakkemaskinerne sikrer, at poserne er forsvarligt lukket, inden de automatisk pakkes i kartoner og kører ud på paller og wrappes.
Under hele processen er der medarbejdere der betjener og overvåger maskinerne – og selvom anlæggene er fuldautomatiserede, er der fortsat behov for at løfte eller trække emner ved fx skift af værktøjer eller folie. Og dermed er der behov for, at sikkerheden er i top for medarbejderne, der arbejder ved maskinerne.